Master the Art of Selecting the Best Lifting Products for Your Business
In today’s fast-paced business landscape, the demand for efficiency and productivity drives companies to invest in high-quality Lifting Products. Whether you’re in the manufacturing, warehousing, or logistics sector, selecting the right lifting equipment is crucial for enhancing operational performance and ensuring worker safety. The right tools not only streamline processes but also reduce the risk of injuries and equipment damage. With a myriad of options available on the market, understanding how to choose the best lifting products tailored to your specific needs can be daunting. This blog will explore the key factors to consider when selecting lifting solutions, from understanding load capacities to evaluating safety features. By mastering the art of selecting lifting products, your business can maximize productivity while fostering a safe and efficient work environment.
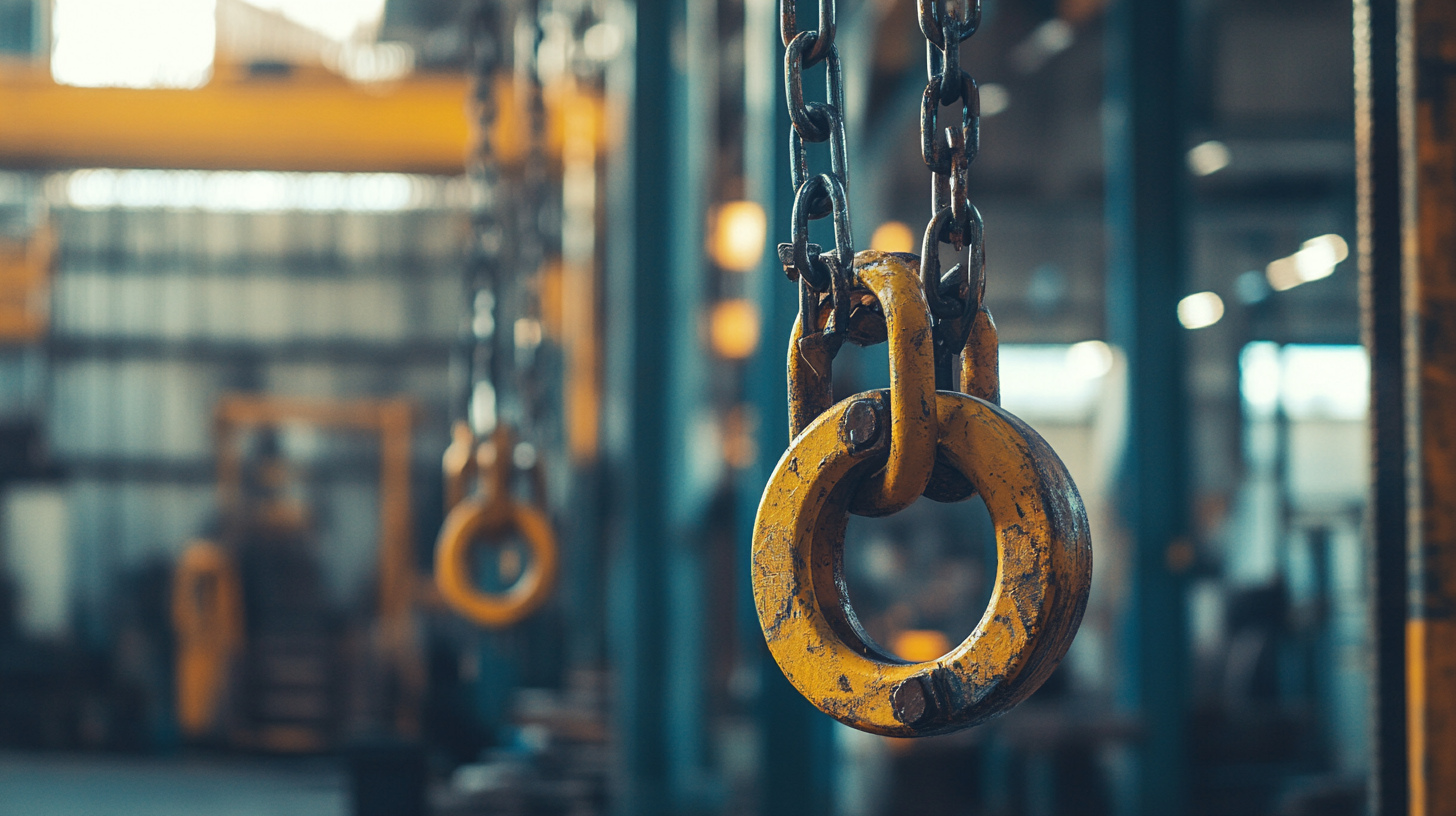
Understanding Different Types of Lifting Equipment and Their Applications
When it comes to selecting the best lifting equipment for your business, understanding the different types of lifting products available is essential. There are several specific categories of lifting equipment, each designed for unique applications. For instance, forklifts are perfect for transporting heavy pallets in warehouses, while cranes excel in lifting materials at construction sites. Another critical category is hoists, which can be utilized for a variety of overhead lifting tasks, from manufacturing to maintenance, making them extremely versatile.
In addition to these traditional products, advances in lifting technology have led to the proliferation of electric and hydraulic lifts, offering enhanced efficiency and precision. Electric lifts are particularly useful in scenarios requiring repeated lifting tasks, offering ease of use and reduced manpower costs. Hydraulic lifts, on the other hand, are ideal for heavy-duty loads, providing significant lifting power while ensuring safety and stability. By understanding these different types of lifting equipment and their specific applications, businesses can make informed decisions that boost productivity and ensure safety in their operations.
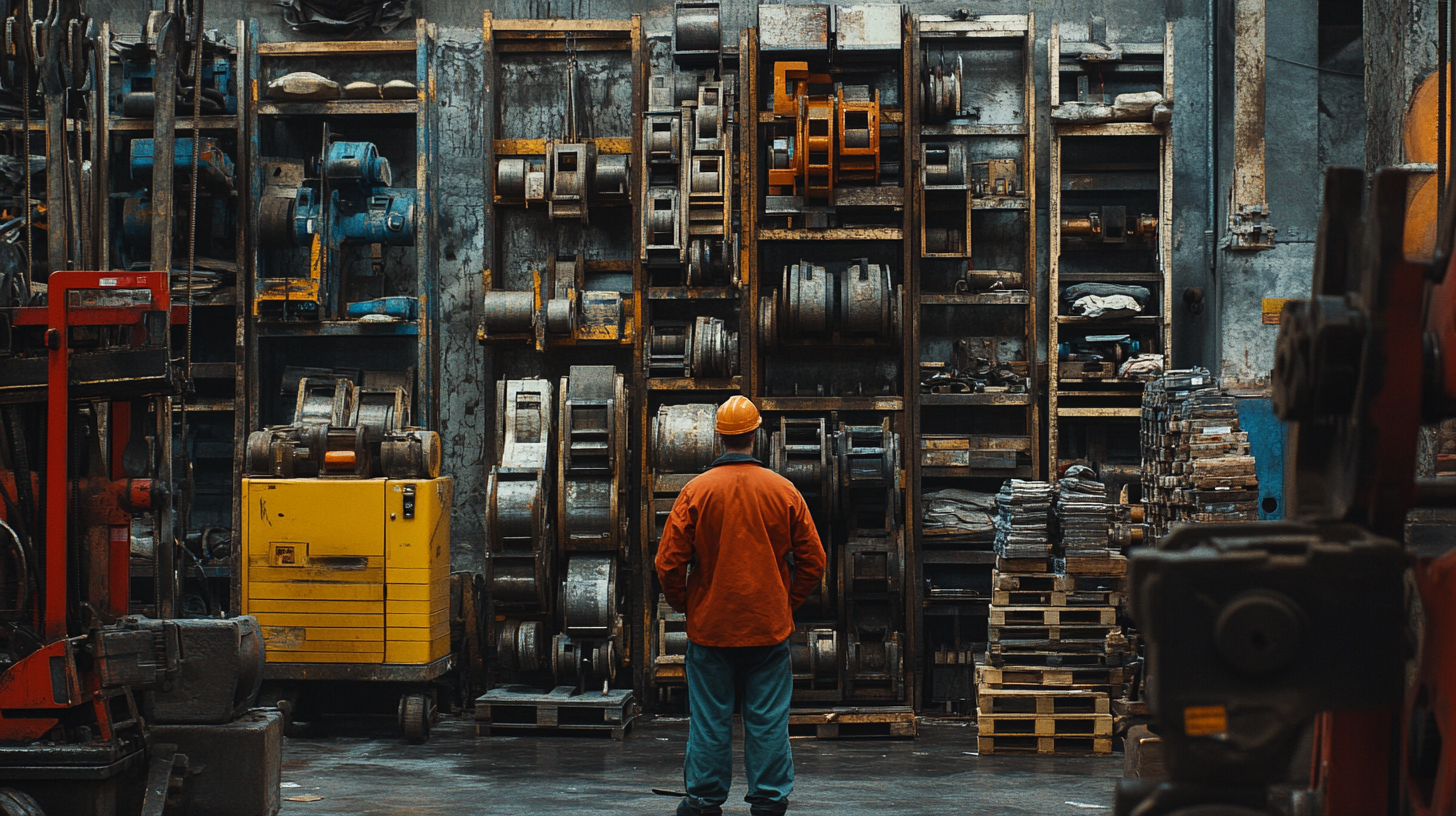
Key Factors to Consider When Choosing Lifting Products for Your Business
When it comes to choosing the right lifting products for your business, several key factors can guide your decision. The first consideration should be the load capacity of the lifting equipment. Assess the maximum weight you will frequently handle and choose products that comfortably exceed this threshold to ensure safety and durability. Remember, selecting a lift that can handle more than your daily needs not only prolongs its lifespan but also safeguards your workforce.
Another critical factor is the type of lifting mechanism. Depending on your industry and specific tasks, you might opt for electric lifts, hydraulic systems, or manual options. Electric lifts are ideal for heavy lifting over longer periods, while hydraulic lifts offer efficiency and strength in tight spaces. It's essential to match the lifting equipment to the nature of your work environment to optimize productivity.
Lastly, consider the ergonomics of the lifting products. Equipment that is designed with user comfort in mind can reduce fatigue and the risk of workplace injuries. Look for products with adjustable features, simple controls, and safety mechanisms. Investing in ergonomically sound lifting products not only enhances efficiency but also promotes a safer, healthier work environment.
Master the Art of Selecting the Best Lifting Products for Your Business
Evaluating Safety Standards and Compliance Requirements for Lifting Gear
When it comes to selecting lifting products for your business, evaluating safety standards and compliance requirements is paramount. Safety gear such as slings, hoists, and cranes must meet established guidelines to ensure a safe working environment. Begin by familiarizing yourself with relevant standards from organizations like ASME and OSHA, which provide essential guidelines for various lifting equipment. This will not only protect your employees but also reduce potential liabilities.
**Tip**: Always look for products with certification marks indicating compliance with safety standards. This verification can prevent accidents and save costs associated with workplace injuries.
Moreover, consider the specific operational environment of your business. Conditions such as extreme temperatures, humidity, or exposure to chemicals can impact the effectiveness of your lifting gear. Consulting with suppliers about how their products withstand these conditions is crucial.
**Tip**: Create a checklist of compliance requirements tailored to your industry to ensure no critical aspect is overlooked during the evaluation process. This proactive approach will help you choose the best lifting products that prioritize safety without compromising efficiency.
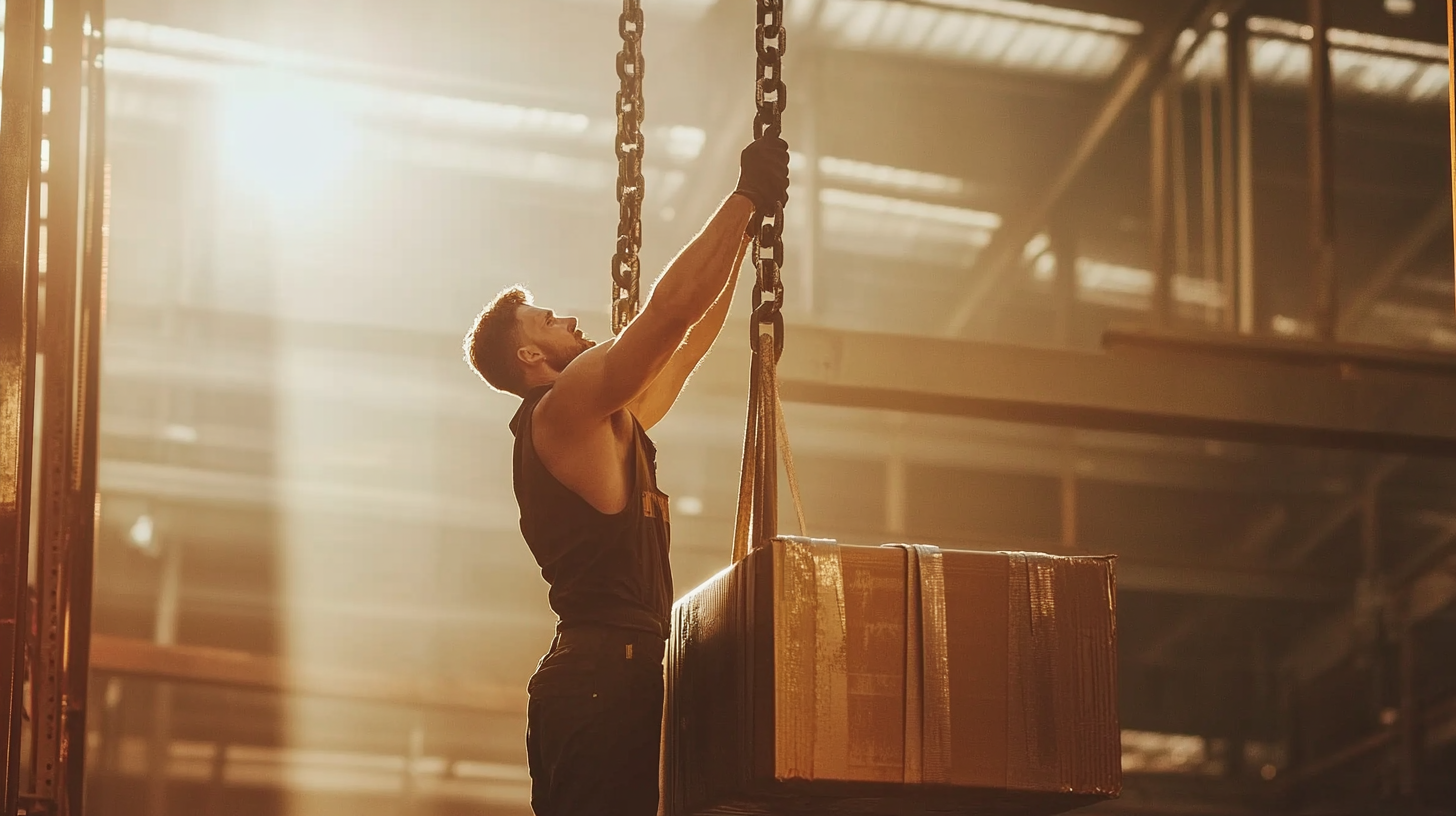
Cost-Effectiveness vs. Quality: Finding the Right Balance in Lifting Equipment
When it comes to selecting lifting equipment for your business, the balance between cost-effectiveness and quality is critical. According to a report by the Material Handling Industry of America, the right lifting solutions can improve operational efficiency by as much as 25%. However, many businesses fall into the trap of prioritizing low upfront costs over long-term durability and safety. Investing in high-quality lifting products often results in reduced maintenance costs and downtime, which can significantly offset initial expenses.
Quality lifting equipment not only enhances safety but also contributes to a better return on investment. Research from the Occupational Safety and Health Administration indicates that workplace injuries related to improper lifting techniques can cost companies an average of $40,000 per incident. Therefore, opting for high-quality, ergonomic lifting solutions can help prevent these costly accidents. Balancing cost with quality means understanding that while low-priced equipment may save money initially, the potential risks and hidden costs could lead to much larger expenses down the line. Emphasizing quality in your lifting equipment choices can ultimately lead to a more productive and safer workplace.
Cost-Effectiveness vs. Quality in Lifting Equipment
Tips for Maintenance and Longevity of Your Lifting Products
Maintaining the longevity of your lifting products is essential for the safety and efficiency of your operations. Regular inspections are key; they help identify wear and tear before it becomes a critical issue. Establish a routine schedule to examine your equipment, checking for any signs of damage, such as fraying cables or faulty hydraulics. Keeping a detailed maintenance log not only helps track these inspections but also aids in making informed decisions regarding repairs or replacements.
In addition to routine checks, proper storage is crucial in extending the lifespan of your lifting products. Ensure that equipment is stored in a clean, dry environment away from direct sunlight and harsh chemicals that can cause corrosion. Limiting exposure to extreme weather conditions can also reduce wear. When not in use, consider covering your lifting products to protect them from dust and debris. Lastly, provide training for your staff on the correct usage of lifting equipment. Proper handling significantly minimizes the risk of accidental damage and ensures that your lifting products perform optimally for years to come.
Master the Art of Selecting the Best Lifting Products for Your Business - Tips for Maintenance and Longevity of Your Lifting Products
Criteria | Details | Maintenance Tips | Expected Lifespan |
---|---|---|---|
Capacity | Ensure the lifting product can handle the maximum load | Regularly check weight limits | 5-10 years |
Material Quality | Select durable materials like steel or high-grade composite | Inspect for rust or wear regularly | 10-15 years |
Safety Features | Look for features like overload protection and emergency stops | Test safety features monthly | Indefinite with proper care |
Ease of Use | Products should be user-friendly and ergonomic | Train staff on proper use | 5-10 years |
Manufacturer Reputation | Choose reputable brands known for quality | Stay updated on recalls and reviews | Variable based on brand |