Unlocking Efficiency in Logistics with the Best Lifting and Handling Equipment Techniques
In today’s fast-paced logistics industry, the effective use of Lifting And Handling Equipment has become paramount to enhancing operational efficiency and reducing costs. According to a recent industry report by McKinsey, companies that optimize their handling practices can reduce logistics costs by up to 20% while also improving service delivery times by 30%. As supply chains become increasingly complex, adopting advanced lifting techniques and equipment is crucial for facilitating the seamless movement of goods. Moreover, a survey conducted by the Material Handling Industry of America (MHIA) found that 75% of companies are investing in innovative lifting solutions to address workforce shortages and meet growing demand. This blog explores various examples of effective lifting and handling strategies that can transform logistics operations, driving efficiency and fostering a safer work environment.
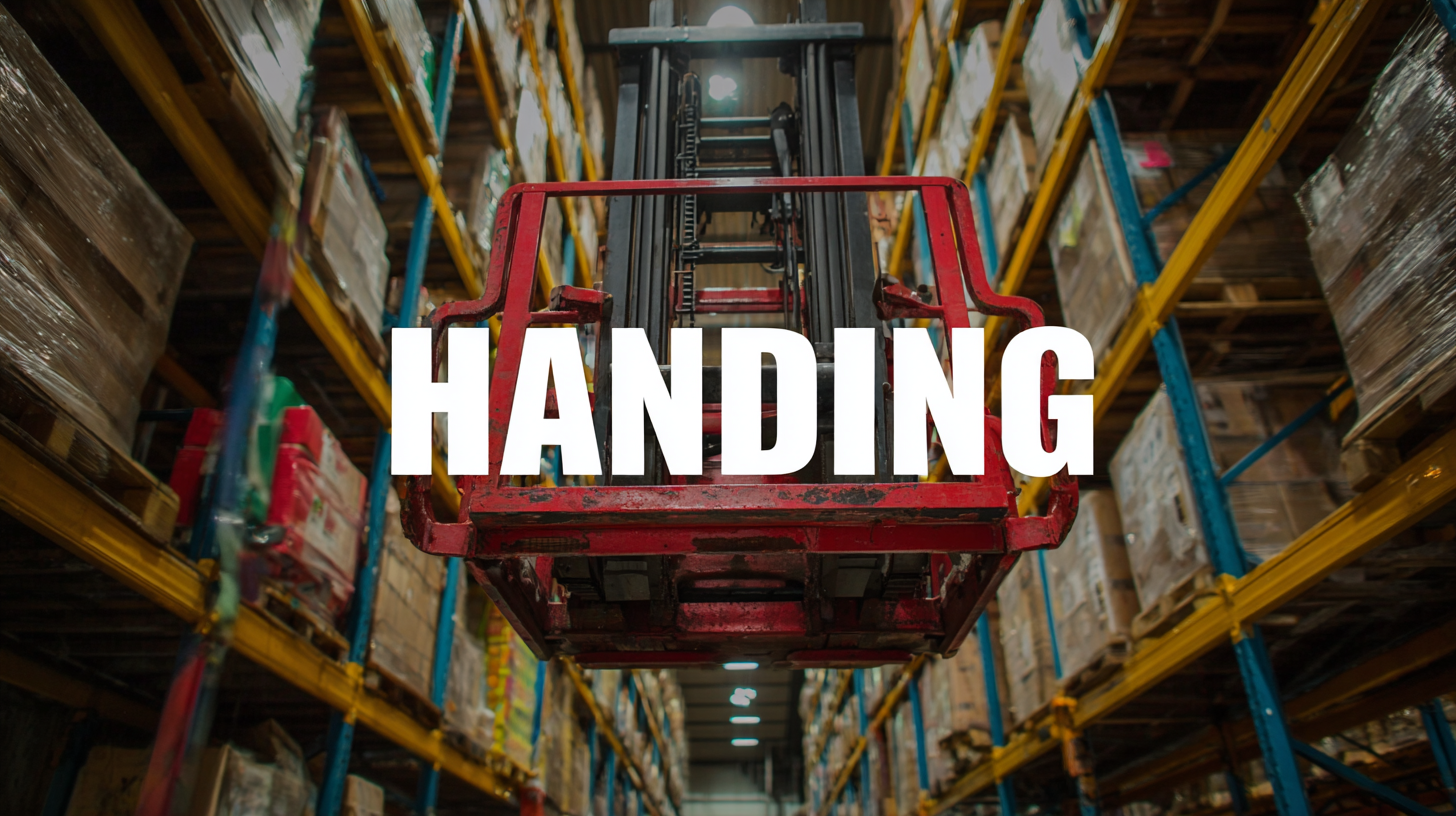
Identifying Key Lifting and Handling Equipment for Your Logistics Needs
In the ever-evolving world of logistics, selecting the right lifting and handling equipment is crucial for optimizing operations and ensuring safety. Understanding the specific needs of your logistics framework is the first step in identifying key equipment. For instance, if your operations involve moving heavy pallets, investing in forklifts or pallet jacks can significantly enhance productivity. For warehouses with high shelving, elevating platforms or cherry pickers may be essential to facilitate safe and effective inventory management.
Furthermore, the type of material being handled plays a critical role in equipment selection. For delicate items, specialized lifting devices, such as vacuum lifts or ergonomic hand trucks, can prevent damage and ease the maneuvering process. Incorporating flexible handling solutions, such as conveyor belts and automated guided vehicles (AGVs), can also streamline processes and reduce manual labor. By carefully assessing your logistics needs and selecting the appropriate lifting and handling equipment, businesses can unlock greater efficiency, improve safety, and drive overall performance.
Assessing the Best Techniques for Safe and Efficient Material Handling
In the fast-paced world of logistics, the efficiency of material handling directly impacts productivity and safety. Assessing the best techniques for safe and efficient material handling is paramount for businesses looking to optimize their operations. One of the foremost techniques is the use of ergonomic lifting tools, which can significantly reduce the physical strain on workers. Implementing equipment such as hoists, forklifts, and pallet jacks with ergonomic features not only enhances productivity but also minimizes the risk of injuries, ensuring a safer workplace.
Additionally, integration of automated systems like conveyor belts and robotic arms can streamline the handling process. These technological advancements allow for quicker movement of goods, reducing downtime and human error. Regular training for employees on handling techniques and equipment operation is equally vital. Well-trained staff can leverage these tools effectively, adhering to best practices that promote both safety and efficiency. Ultimately, by focusing on these innovative techniques, companies can unlock significant improvements in their logistics operations.
Unlocking Efficiency in Logistics with the Best Lifting and Handling Equipment Techniques
Technique | Equipment Used | Efficiency Rating | Safety Rating | Cost Efficiency |
---|---|---|---|---|
Pallet Jacking | Manual/Electric Pallet Jacks | 85% | 90% | High |
Forklift Operation | Counterbalance Forklifts | 90% | 85% | Medium |
Conveyor Systems | Belt Conveyors | 95% | 95% | High |
Cranes | Overhead Cranes | 93% | 80% | Medium |
Robotic Systems | Automated Guided Vehicles | 98% | 90% | Very High |
Developing a Comprehensive Maintenance Checklist for Lifting Equipment
When it comes to lifting and handling equipment in logistics, a comprehensive maintenance checklist is not just beneficial; it is essential for ensuring operational efficiency and safety. Regular maintenance not only extends the life of the equipment but also minimizes the risk of accidents caused by malfunctions or improper handling. A well-structured checklist should include daily inspections, weekly performance evaluations, and periodic deep dives into mechanical and electrical systems. This proactive approach can help identify potential issues before they escalate into costly repairs or downtime.
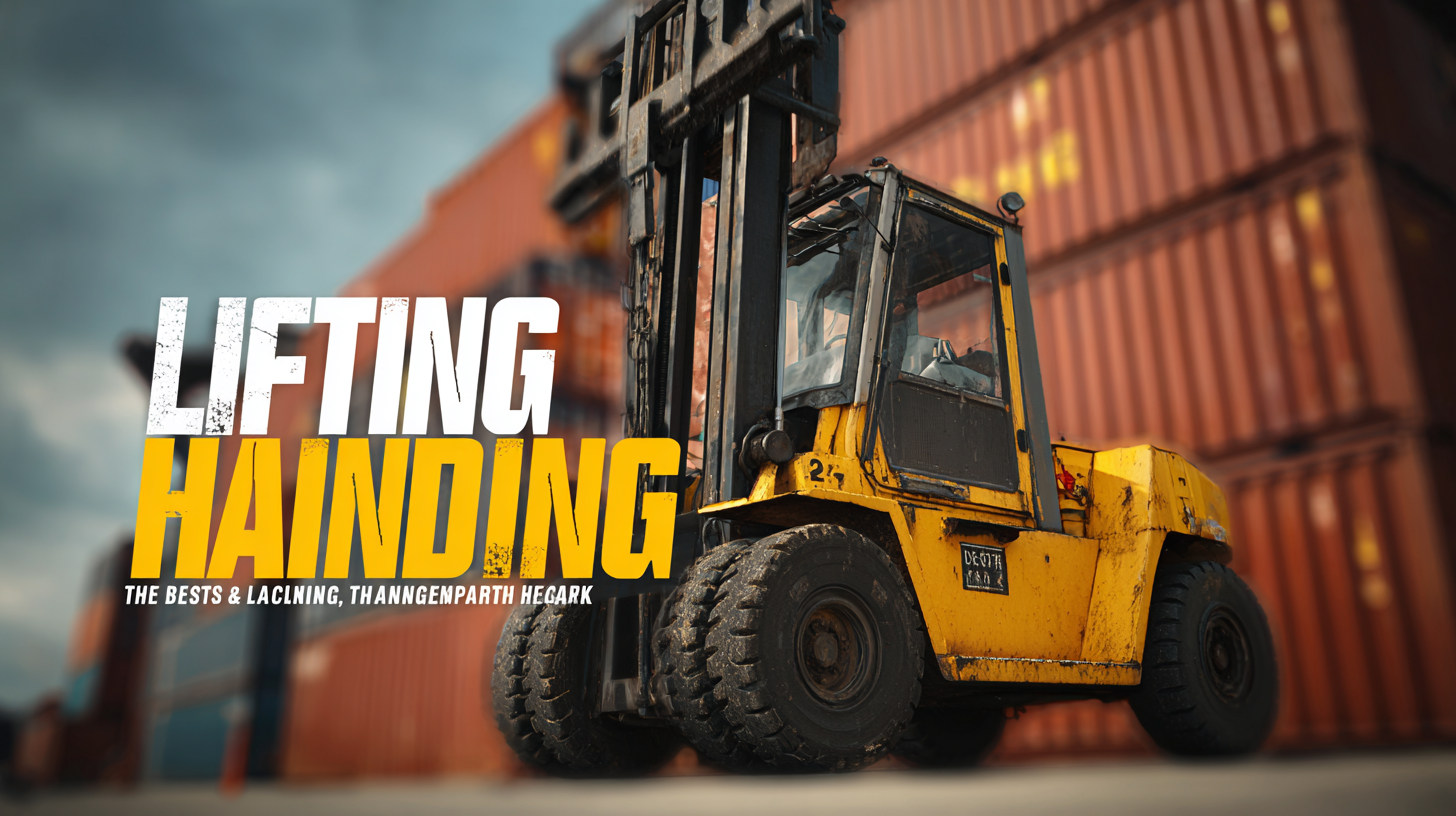
In crafting a maintenance checklist, it’s important to focus on key areas such as load capacity checks, wear and tear assessments, and lubrication schedules. Incorporating technology, such as RFID tags or maintenance management software, can streamline tracking and reporting for maintenance activities. Additionally, training employees to recognize signs of equipment wear and to adhere to maintenance protocols fosters a safety-first culture. By prioritizing a thorough maintenance strategy, logistics companies can unlock improvements in efficiency, reduce liability risks, and enhance overall productivity in their lifting and handling operations.
Training Employees on Proper Use of Lifting Devices and Safety Protocols
In today's fast-paced logistics industry, ensuring the safe and efficient use of lifting and handling equipment is paramount. Proper training for employees not only enhances productivity but also significantly reduces the risk of workplace accidents. According to a report by the Occupational Safety and Health Administration (OSHA), improper handling of materials is responsible for nearly 25% of workplace injuries, highlighting the critical need for comprehensive training programs. By equipping employees with the knowledge of safety protocols and proper usage techniques, companies can foster a safer working environment.
Moreover, effective training on lifting devices can lead to a notable decrease in operational downtime. A study from the National Safety Council states that businesses can save approximately $4.3 billion annually in injury-related costs by investing in proper employee training. This investment pays off not just in reducing injuries but also in improving overall efficiency and employee morale. Providing hands-on training sessions and regular refreshers ensures that employees are always up-to-date with the latest safety practices, which is essential in an industry where the stakes are high and efficiency is vital.
Evaluating the Impact of Technology on Lifting and Handling Efficiency
In today's fast-paced logistics landscape, the integration of advanced technology in lifting and handling equipment has significantly enhanced operational efficiency. Modern tools, such as automated guided vehicles (AGVs) and advanced pallet jacks, are revolutionizing traditional methods, allowing for smoother workflows and improved safety. By automating repetitive tasks, businesses can focus their workforce on more complex operations, ultimately driving productivity.
Tip: Incorporate IoT-enabled devices to monitor equipment performance in real-time, allowing quick adjustments to workflows as needed. This proactive approach not only minimizes downtime but also increases the lifespan of your equipment.
Moreover, software solutions like warehouse management systems (WMS) provide real-time data analytics on lifting and handling operations. This empowers managers to make informed decisions and streamline processes. The right software can identify bottlenecks and inefficiencies, ensuring that the lifting and handling equipment is utilized to its fullest potential.
Tip: Regular training sessions on new technologies and equipment for your workforce can lead to improved handling techniques, ensuring safety and efficiency. An informed team is pivotal to maximizing the technology investments made in lifting and handling processes.
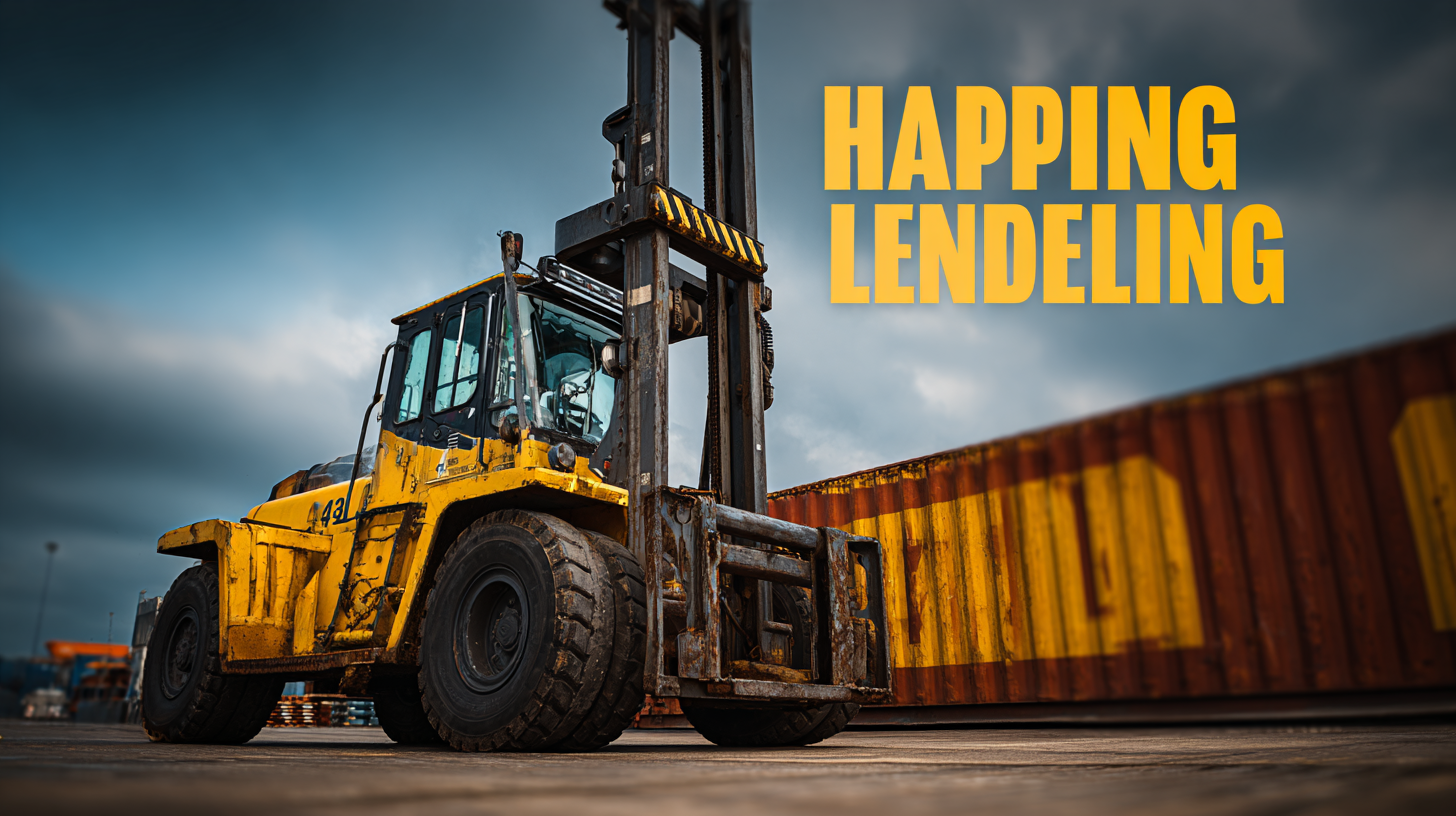